___________________________________________________________________________________________________
“And in the end, it’s not the years in your life that count. It’s the life in your years.”
— Abraham Lincoln
___________________________________________________________________________________________________
Sometime this week we are going to open the pre-order window for our new HP6v2 Tapered Sliding Dovetail System. Thanks to all who commented last week regarding this tool. This has really been a rewarding project–the very thought of making an extraordinarily difficult joint brain-dead easy really excites me.
Because this concept is new, actually foreign might be more descriptive, I thought it would be helpful to answer some of the many questions that we have received (in addition to those unanswered questions on this Totally Awesome and Worthless blog)…in no particular order
Why did you spend time developing this tool?
Tapered sliding dovetails are almost always made with a router, and that is how I made them years ago. I thought the HP6v2 could do the job, and always wondered why the traditional methods left so much to be desired. It is a hard tool to do research on but I did find a little tidbit in The Handplane Book by Garrett Hack where he does not share much love for the Stanley 444. I have never seen this plane up close and personal but the solution seems primitive to me. I don’t know, I just assigned myself the challenge of finding an easy solution–it is an incredibly useful joint that is grossly underused.
Will this system do stopped dovetails?
Yes but it is not obvious. Simply band or add material to the edge where you do not want to see the joint after assembly. This will take a bit of planning but works well.
Can I make dovetails shorter than .300″?
Yes, but you are on your own in making the shims for the soles. Totally doable.
What if I don’t want centered dovetails?
No problem–you just need to figure out your centerlines. This entire system works on centerlines.
Does the joint lock together where I might not need glue?
A 1/2 degree tapered dovetail self-locks and frankly they sometimes are easier to assemble than take apart. So yes it locks.
Can you go through the steps again?–I have read your blog a dozen times and it is still not completely clear how this works to me.
You start by making the male dovetail first as in ALWAYS. There is no debate here. The dovetail sole of the HP-6v2 is fixed to cut a dovetail that is 0.300″ tall. You set the iron to cut about 0.005″ (it cuts from the side, not the bottom) and attach either one or two tapered dovetail guides to your stock with clamps. Next identify the end of your stock that will be at the back (we always slide dovetails from back to front). Next, you will set the fence so the cutter just makes a clean dovetail at the back (the dovetail gets narrower towards the front). The idea (most of the time) is to remove as little material as possible. Cut until the plane quits cutting and repeat on the other side–when completely, your tapered sliding make dovetail will be centered on your stock.
Now we empirically determine the narrow dovetail width using the dovetail gage. This gage needs to be flush with the front of your stock. Lock in place and slide off.
Using a caliper, measure the distance between the flanges on the top of the dovetail gage. This is the width of the groove you need to make for the female dovetail.
Let’s say that width is .582″. At this width you need the 1/2″ dado in the HP-6v2, under .5″ you use the 3/8″ dado kit. (We really do recommend using a second body for this joint to avoid breaking down and resetting the dovetail kit.) Retract the iron, set it in the setup gage and drop the depth fences to the top of the gage and lock all four screws. Next set the iron to cut about 0.002″.
Using our new Adjustable Fence, set the Vernier to 0.00″. Using a square, lock the fence exactly 1″ away from the centerline where you want the female dovetail.
Now here is the really cool part; once the fence is clamped to your stock, adjust the fence 0.041″ (one half of 0.082″–we are only dealing with the material in excess of .5″). And make your first complete plow cut. When complete, adjust the fence to the exact same setting on the other side of zero and make the remaining groove cut. Your 0.582″ wide groove is now complete and centered. How cool is that? You NEVER need to unclamp the fence from your stock.
Take the locked dovetail gage and place the flange into your groove–it should fit perfectly, a nice, no wiggle fit. Make sure it is flush with the front face of your stock and the arrows are aligned correctly indicating that the gage sides are indeed narrow at the front and wide at the back.
Next, clamp some straight wooden guides to your stock with the edges aligned with both edges of the dovetail guide. This guide knows the “geometry” of the dovetail sole. Once the guides are in place, start cutting until the sides of the plane rub on the guides and quit cutting. That is it. Your joint should go together dead perfect.
John, I don’t like the idea of setting the tapered dovetail guide with that red gage. It looks like a major pain in the ass. Can’t you do better?
I hear you. Two changes; one we are going to offer the tapered guides in two lengths, 12″ and 24″ so you have a choice. And for those that don’t want to do two clamp ups for a single male dovetail, we have modified the design as below, the little orange hangers will be an accessory for those that want them. Once clamped, slide them off and plane up one side and down the other with two guides clamped in place. And for you picky DSN members, here are the guides in gray… we may go back to purple just to be ornery.
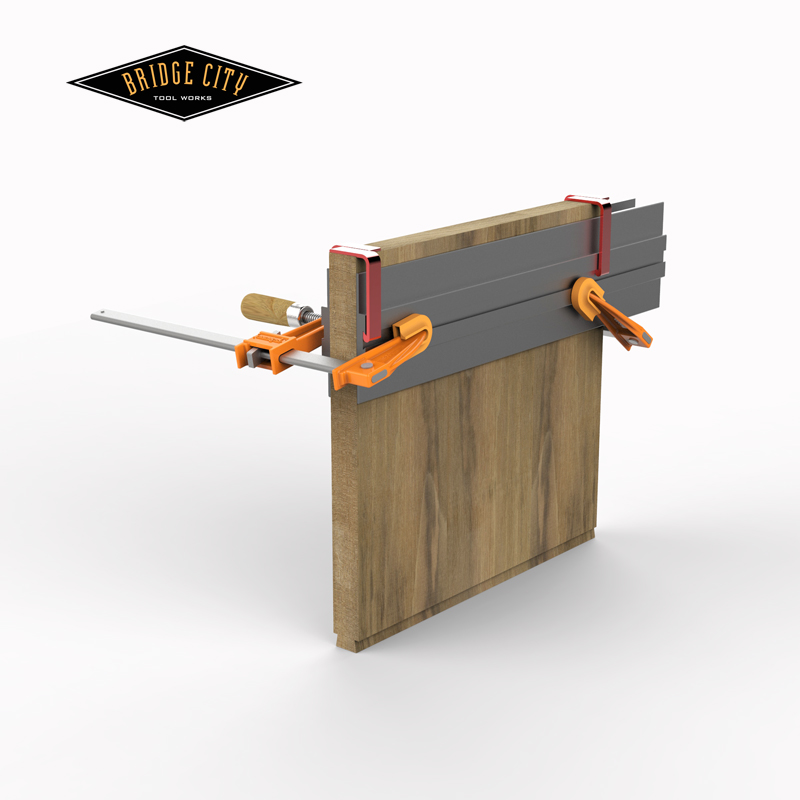
I don’t understand the geometry of the iron–care to explain??
First, the dovetail walls are 10 degrees off vertical. The iron is bedded at 55 degrees in the HP-6v2 body. The “V” groove combined with a 15 degree back bevel creates an edge angle of 26.6 degrees, and we do not use a micro-bevel.
The iron works exactly like a skewed block plane, and in this case, the skew is 35 degrees. Combined with the bed angle of 55 degrees, the actual attack angle of the edge is 40.2 degrees. This is a great compromise for doing the male and female cutting of the joint. Here is an example of how much little material is actually removed to create the dovetail–depending on your material and blade setting, it might take anywhere from 8-15 passes per side, but they are light passes;
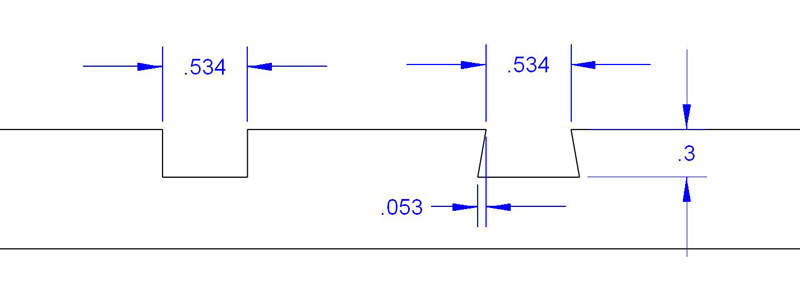
“Where do the shavings go?
Think of the HP-6v2 Dovetail Kit as a block plane on it’s side. The front throat is adjustable and shavings exit the other side which has been relieved for that purpose.
“How long will that little scoring cutter last?
I don’t know–depends on the material and frequency of use. It does not spin, so when it gets dull, rotate it about a 10 degrees.
“Will the tapered sliding dovetail kit fit the old brass body?
No.
“What can go wrong using this system?
From a math perspective, and as long as our components are in tolerance, any error will be user error.
“Will spare irons be available?
I tried my hardest to make this a dual iron but it didn’t work out. Now, this may come across as blatant hucksterism, but this is one kit where we actually recommend a spare iron. There I said it.
Thanks for the questions! If you have more let us know and I will update this post. Lastly, we are really excited about this plane kit. Literally one of the most difficult joints to do by hand is now almost as easy as a rabbet joint. The secret is this little iron, which by the way, now will allow us to design a kit for making “T” slots in wood. 🙂
–John